Have you ever thought about how is a chair made? The creation of a chair involves multiple components that collectively give it the appearance you recognize. The design can vary from resembling others closely to exhibiting significant differences.
However, the underlying principles stay consistent. To streamline production in a factory, a solitary chair is disassembled into individual parts. These components then undergo an assembly process, ultimately transforming into the finalized product.
- Initial step: design for safety, assess stability, tipping, rocking.
- Collect various components like bolts, nuts, foams, fabrics from different sources.
- Separate design of back, legs, seat, armrests. Cushioned chairs involve stuffing, coil springs, outer covering.
- Assembly with rubber footing for scratch prevention.
- Finish for wooden surface protection. PU coating for durable protective layer. Upholstery chemical treatment for stain resistance.
Mass production is implemented to reduce costs, leveraging economies of scale through the bulk procurement of raw materials, ultimately ensuring competitive pricing.
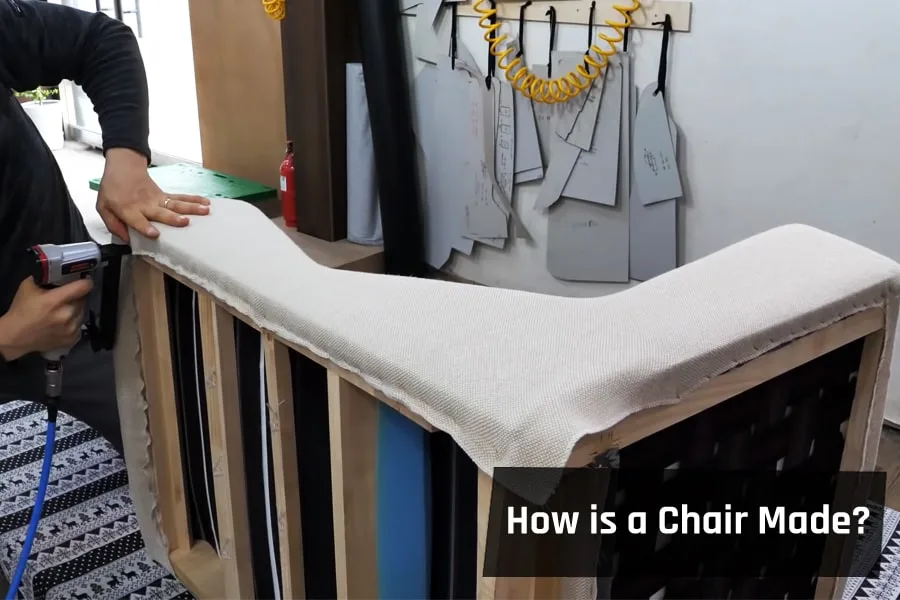
How is a Chair Made – Step by Step Process
Find the below step-by-step process of making a chair.
Step 01: Design Phase
The initial step in crafting a chair involves the design phase. Given the integral role chairs play in our daily lives, ensuring safety during use is paramount. The design revolves around assessing the chair’s stability and safety when someone sits on it.
Factors such as tipping over or rocking side-to-side are carefully considered in this phase.
Typically, the initial design is hand-drawn, and a prototype is constructed using scrap lumber to validate stability and safety. Larger companies often employ computer-aided design (CAD) to facilitate quick adjustments in case of design flaws.
Step 02: Pre-Assembly Phase
As mentioned earlier, a chair comprises various components, some sourced from different manufacturers.
While bolts, nuts, foams, and fabrics may come from external suppliers, key components like wooden parts are typically crafted in-house.
In the factory, individual chair components, including the back, legs, seat, and armrests, are designed separately during this phase.
Step 03: Assembly Phase
Chairs exhibit diverse forms and styles, each requiring a specific assembly method. The factory meticulously studies the components and design before determining the most efficient assembly method.
The sequence in which components are assembled is carefully planned to minimize wastage and reduce assembly time.
Chairs with cushioning involve processes like stuffing or loading coil springs before applying the outer covering. The back, armrests, and legs are then assembled with the seat, incorporating additional rubber footing to prevent scratches or abrasions.
Step 04: Post-Assembly Phase
To safeguard against potential damage, a finish is applied to the wooden surface, categorized as either penetrating or surface finish. Penetrating finishes seep into the wood, providing a more natural appearance.
Surface finishes, such as PU coating, create a durable protective layer suitable for wood furnishings subjected to wear and tear. Upholstery materials or fabrics may undergo chemical treatment to resist stains.
Step 05: Finished Phase
Having undergone a meticulous manufacturing process, the wooden chair reaches its finished phase. Adhering to strict manufacturing procedures ensures that the chair is suitable for shipment and can be packed into carton boxes for transport.
Internal quality control may randomly select sample chairs for testing to validate that the finished product meets expectations. With proper care, a well-crafted wooden chair can endure for years or even generations.
What are the materials used to make a chair?
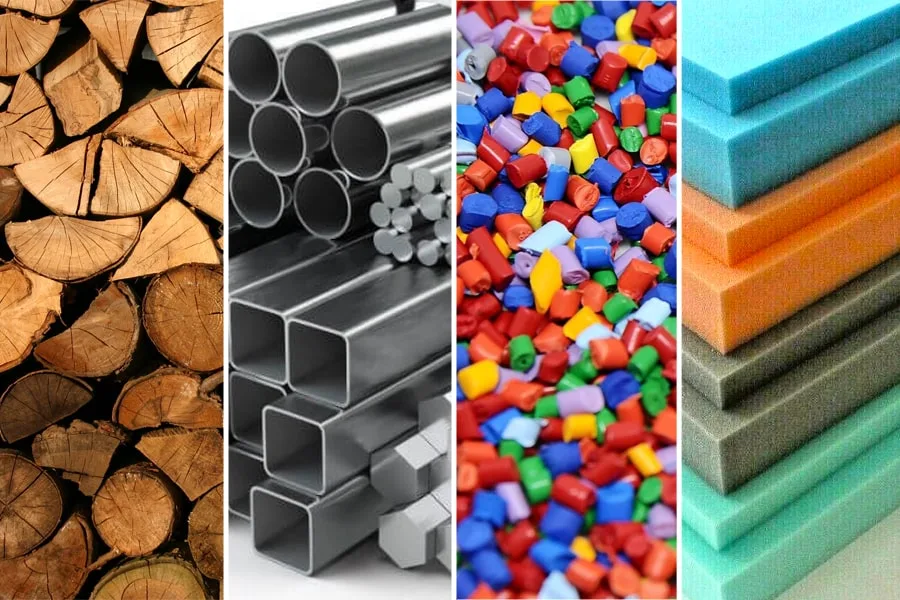
The combination of the below materials allows for a wide variety of chair designs, each catering to specific preferences, styles, and functional requirements.
Wood
- Solid wood: Often used for chair frames, legs, and other structural components.
- Plywood: Layered wood sheets glued together, providing strength and stability.
- Veneer: Thin layers of wood applied to surfaces for decorative purposes.
Metal
- Steel: Commonly used for chair frames and legs due to its strength and durability.
- Aluminum: Lightweight and corrosion-resistant, suitable for outdoor or modern designs.
- Iron: Sturdy material, often used for decorative elements in chairs.
Plastic
- Polypropylene: Lightweight, durable, and versatile, frequently used for modern and outdoor chairs.
- Polyethylene: Known for its flexibility, often used in molded and ergonomic chair designs.
- Acrylic: Transparent or colored plastic used for contemporary and stylish chair designs.
Upholstery Materials
- Fabric: Various textiles, such as cotton, linen, or polyester, used for chair seat and back covers.
- Leather: Provides a luxurious and durable covering for chairs.
- Vinyl: Synthetic material with similar properties to leather, often used as a cost-effective alternative.
Foam and Padding
- Polyurethane foam: Commonly used for cushioning in seats and backs.
- Memory foam: Offers enhanced comfort by molding to the shape of the user.
- Batting: Soft material placed between upholstery and frame for added comfort.
Fasteners
- Bolts and Nuts: Secure metal parts together, ensuring structural integrity.
- Screws: Used for assembling various components and attaching hardware.
- Staples: Commonly employed in attaching fabric or upholstery to the chair frame.
Finishes and Coatings
- Paint: Applied to wooden or metal surfaces for aesthetic appeal and protection.
- Stain: Enhances the natural color of wood while providing a protective layer.
- Varnish: Clear coating applied to wood for protection and a glossy finish.
Other Decorative Elements
- Glass: Used for tabletops or decorative insets in certain chair designs.
- Rattan or Wicker: Natural materials used for weaving chair seats and backs in some styles.
Here is a table outlining the common materials used in the construction of various types of chairs, highlighting the frame material, seat/back material, and additional components specific to each chair type.
Keep in mind that variations may exist within each chair category, and materials can be adapted based on design preferences and manufacturing considerations.
Chair Type | Frame Material | Seat/Back Material | Additional Materials |
Wooden Chair | Solid Wood, Plywood | Fabric, Leather, Veneer | Upholstery Foam, Metal Fasteners, Finishes |
Plastic Chair | Polypropylene, Polyethylene | Plastic | Metal (for legs), Rubber Feet, UV Stabilizers |
Office Chair | Steel, Aluminum | Fabric, Mesh, Leather | Casters, Gas Lift Mechanism, Armrests, Foam |
Adirondack Chair | Cedar, Teak, Pine | Wood Slats, Adirondack Style | Stainless Steel Fasteners, Finishes |
Recliner | Wood, Metal | Leather, Fabric | Springs, Reclining Mechanism, Cushioning Foam |
Bean Bag | Nylon, Polyester | Filled with Beans or Foam | Zipper Closure, Double Stitching, Covers |
FAQ
What types of foam and padding are commonly used in chair construction?
Commonly used foams in chair construction include polyurethane foam for seat and back cushions, providing comfort and support. Memory foam molds to the user’s shape for enhanced comfort.
Padding materials like batting are used between upholstery and the frame for added softness and resilience, contributing to the overall seating experience.
How does the design phase impact the safety and stability of a chair?
The design phase determines chair safety by addressing factors like stability, preventing tipping, and ensuring durability.
Final Notes
Hopefully, now you know how a chair is made.
As the world advances, emerging technologies and materials continually aid human life. Plastic chairs and synthetic fabrics gain prominence, revolutionizing living and workspaces.
Dominated by injection molding and CNC, manufacturing accelerates, ensuring higher quality and precision. Wood remains a pivotal furniture raw material, often complemented by synthetics. Consumer choice ultimately determines material preferences.